Jak automatyczny system transportu i magazyn do składowania pojemników poprawił efektywność w firmie z branży motoryzacyjnej
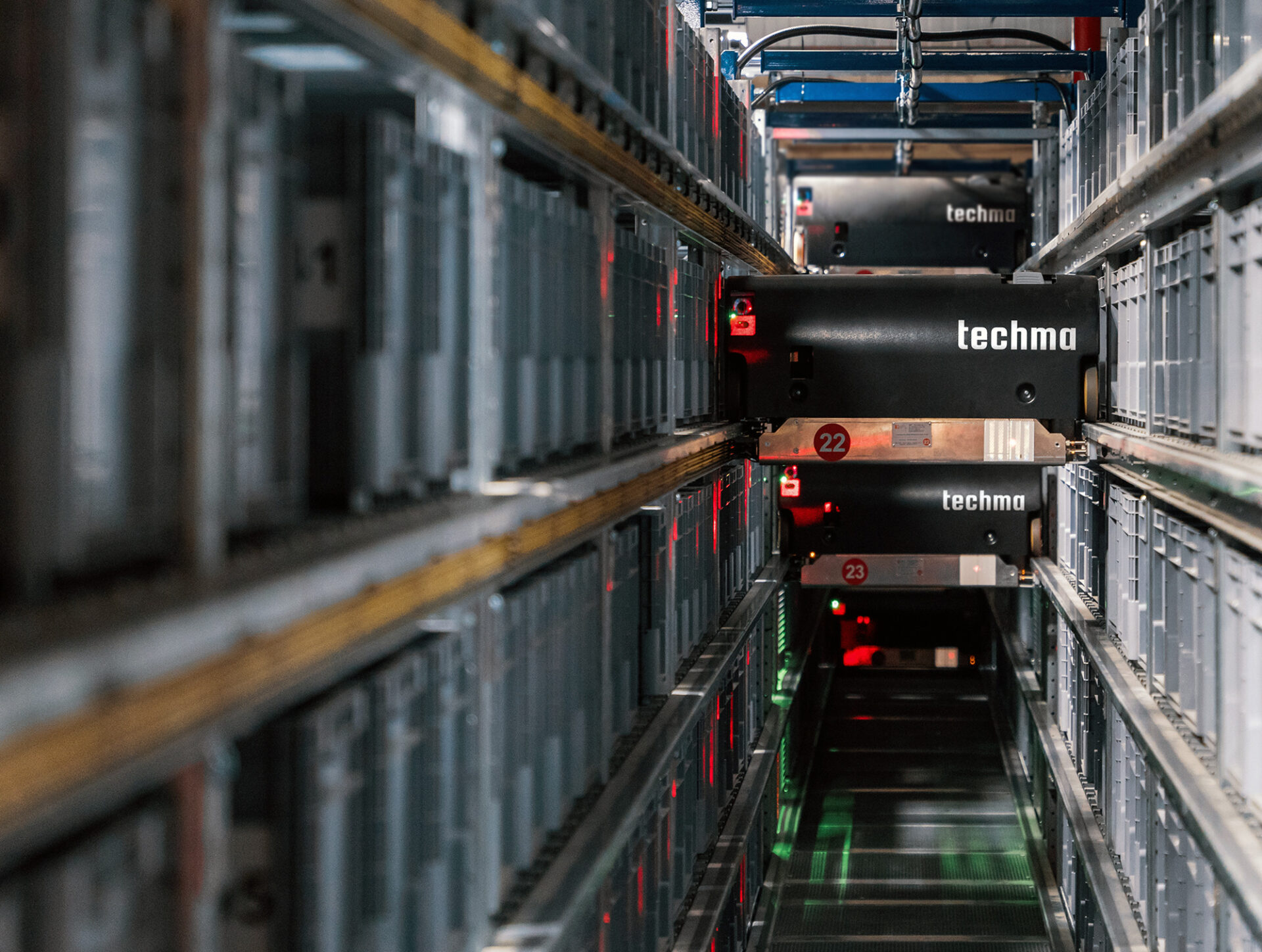
U naszego klienta, który specjalizuje się w imporcie oraz dystrybucji części samochodowych, pojawiła się potrzeba efektywnego zagospodarowania zwrotami oraz dostawami towarów w centrum logistycznym. W tym celu zaprojektowaliśmy dla niego oraz zbudowaliśmy efektywny, automatyczny magazyn wysokiego składowania.
Magazyn na 11 tysięcy pojemników
Na etapie przygotowania koncepcji magazynu otrzymaliśmy opracowaną specyfikacją rozwiązania technicznego. Podczas naszych prac została ona jeszcze bardziej dopasowana do wymagań i potrzeb inwestora.
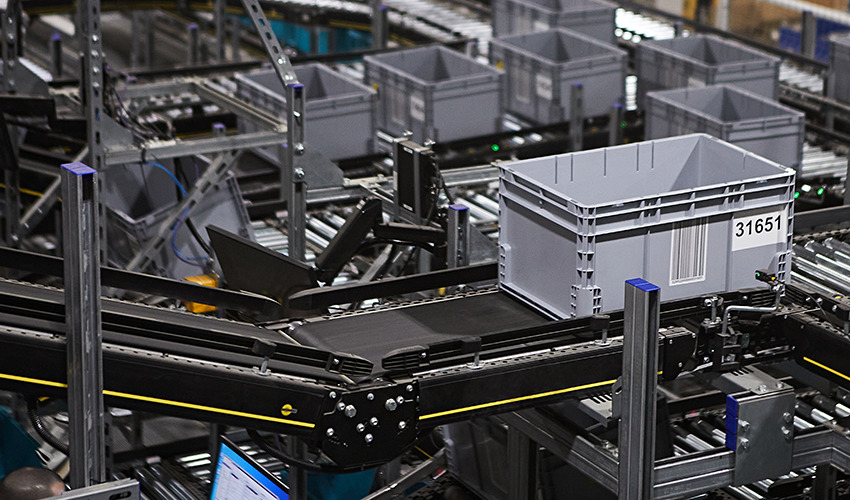
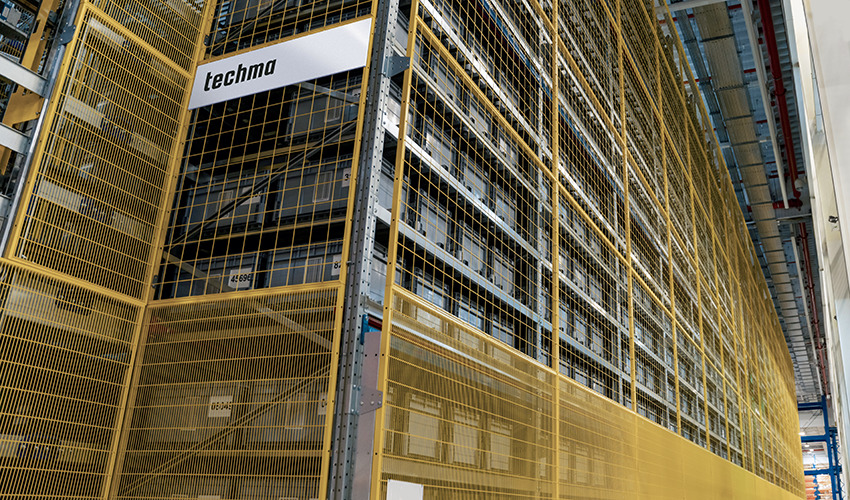
W efekcie powstał automatyczny system, składający się z magazynu wysokiego składowania mieszczący prawie 11 tysięcy skrzynek. Magazyn obsługiwany jest przez 30 automatycznych wózków typu shuttle, 4 miniloady oraz 4 wydajne przenośniki pionowe.
Kolejnymi elementami systemu jest układ przenośników transportujących skrzynki i dwie stacje kompletacji z potrójnymi slotami. Dodatkowo wdrożyliśmy stację błędu z układem ważenia skrzynek wraz z procentowym określeniem ich wypełnienia. Projekt uzupełniliśmy o strefy przyjęcia nowego towaru oraz strefy szybkiej i efektywnej kompletacji.
Na etapie projektowym wykonaliśmy modelowanie procesów logistycznych magazynu przy pomocy narzędzia FlexSim. Stworzyliśmy interfejs komunikacyjny pomiędzy systemem WMS klienta a Scadą Iconics, która odpowiada za alokację i przepływ skrzynek w systemie magazynowym.
Blisko czterokrotny wzrost efektywności
Towary wracające z sieci sklepów oraz nowe towary od producentów są rejestrowane w systemie i umieszczane w skrzynkach w strefie przyjęć na 30 stanowiskach inspekcyjnych. Dalej, są one przenoszone przenośnikami rolkowymi oraz pasowymi do magazynu.
Tam rozwożone są na poszczególne piętra magazynu za pomocą przenośników pionowych, odbierane przez wózki shuttle i umieszczane w wolnych lokalizacjach w systemie double deep.
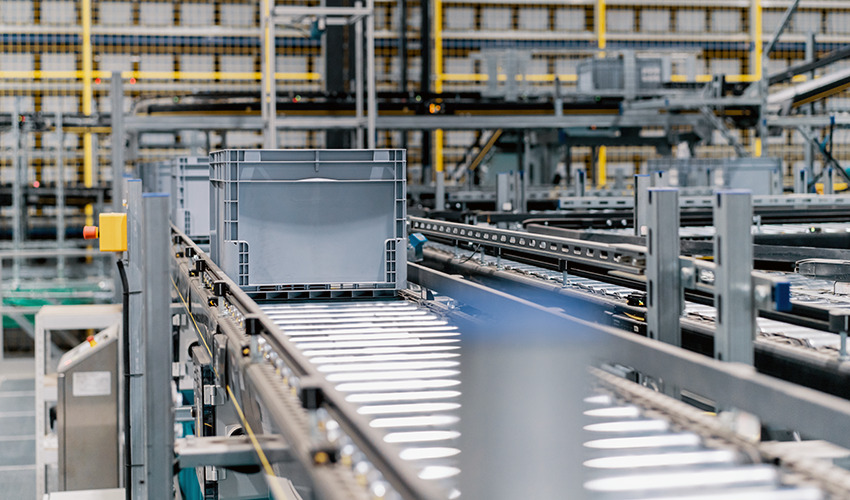
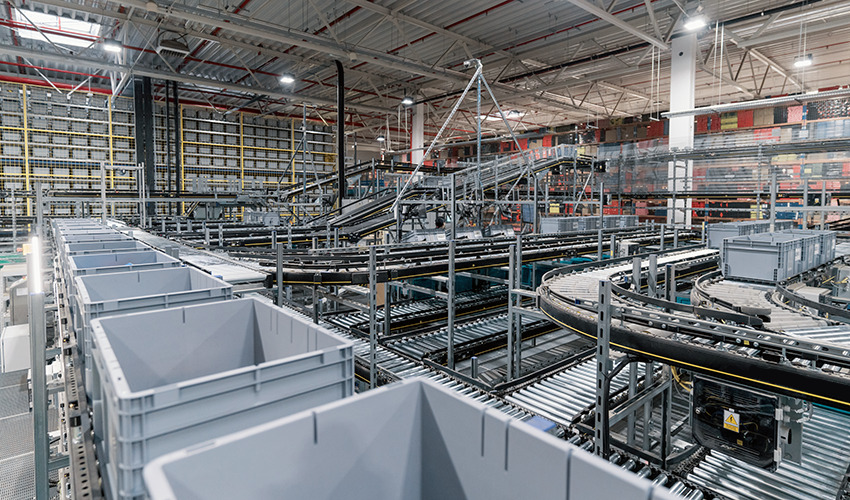
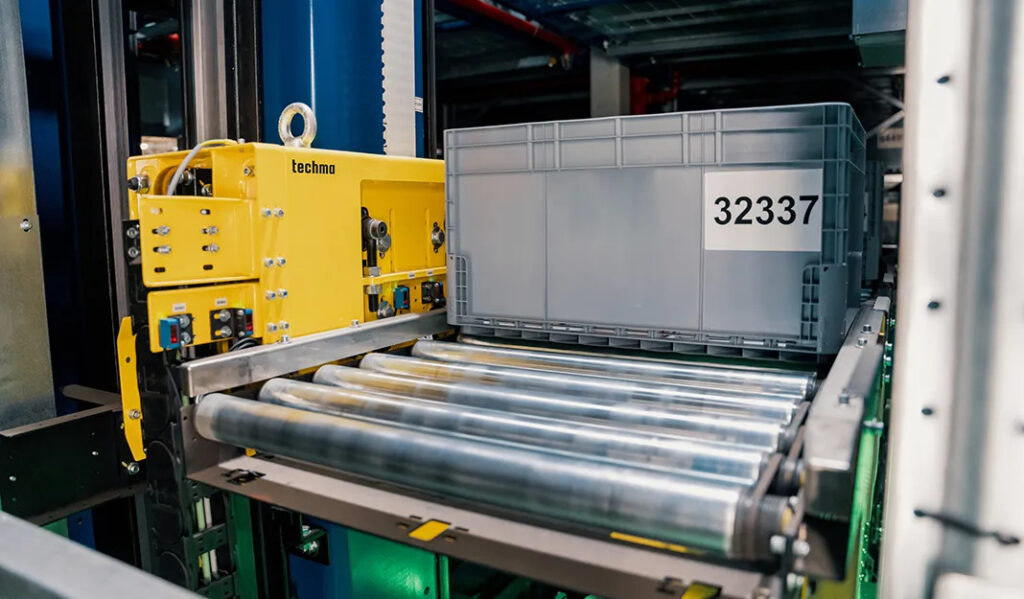
Następnie skrzynki wydawane są z magazynu i transportowane do odpowiednich stanowisk. Maksymalna zmierzona wydajność systemu to 1200 skrzynek wjeżdżających do magazynu i tyle samo wyjeżdżających w ciągu godziny. Inwestor może w dalszym ciągu bez przeszkód korzystać ze swojego systemu WMS, w którym magazyn wysokiego składowania widnieje jako nowa lokalizacja.
Istotną dla klienta cechą była otwartość systemu i zastosowanie komercyjnych podzespołów, które są powszechnie dostępne na rynku.
W naszych rozwiązaniach nie stosujemy sterowania typu black box z dedykowaną elektroniką. Pozwala to na samodzielną diagnozę i serwisowanie magazynu bez długiego czasu przestoju.
Główną korzyścią, jaką otrzymał klient, było dwu-trzykrotne zwiększenie wydajności procesu kompletacji. Pracownicy dokonujący kompletacji zamówień w starszych częściach magazynu zbierają do 80 produktów na godzinę. Natomiast w naszym magazynie pojedynczy pracownik kompletuje 300 towarów w ciągu godziny.
Tekst: Janusz Baranowski, MPL Techma
Zdjęcia: MPL Techma