Case study: Inwestycja w Radzyminie – automatyczny magazyn Jungheinrich dla Coca-Cola HBC
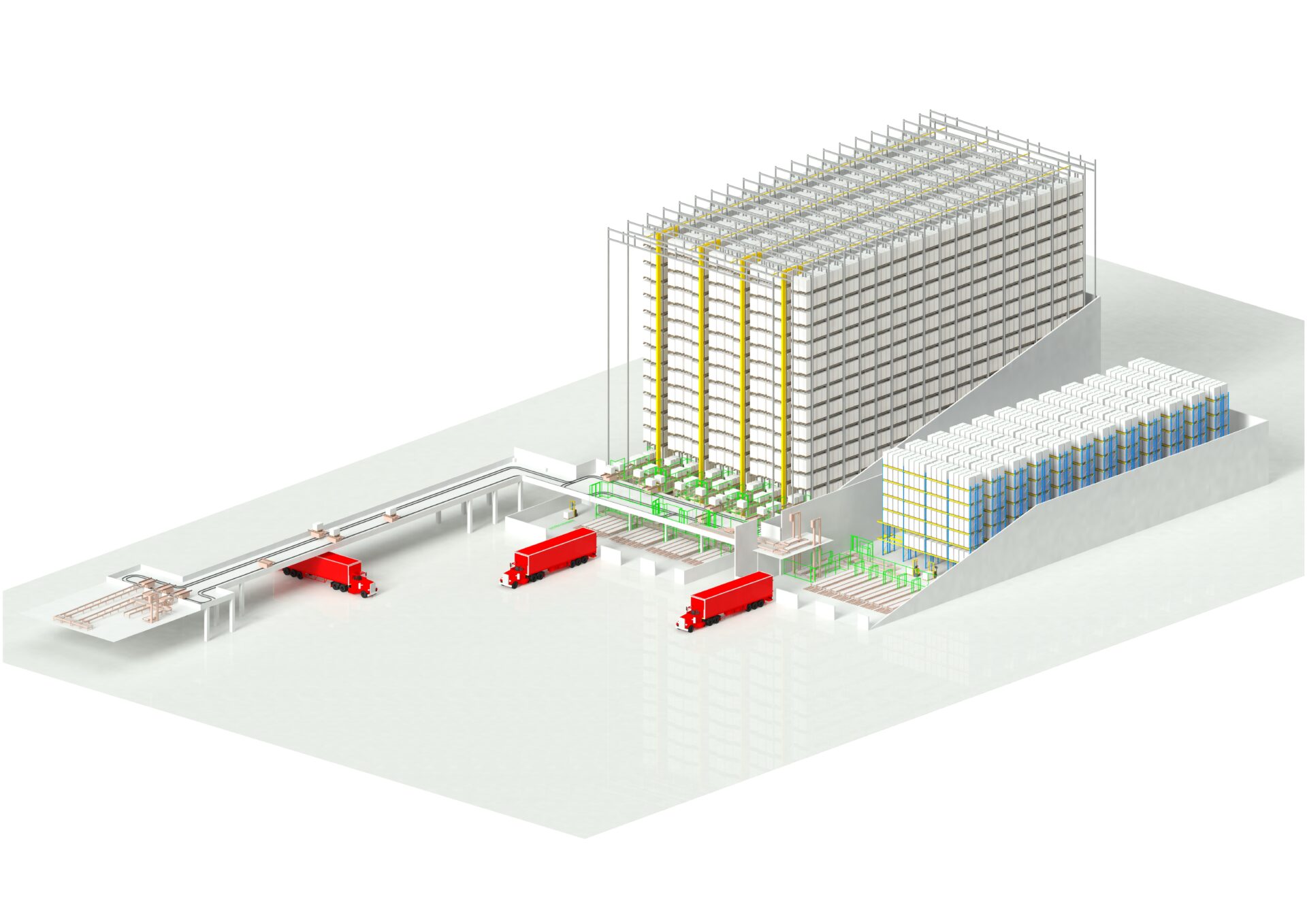
Firma Jungheinrich buduje w Radzyminie automatyczny magazyn dla Coca-Cola HBC. Rozwiązanie obejmuje rozbudowę istniejącego obiektu i wyposażenie go w najnowocześniejszą technologię. Niektóre prace budowlane są przeprowadzane podczas bieżącej działalności firmy. Oddanie do użytku planowane jest w 2022 roku. Celem projektu jest wykorzystanie w pełni dostępnej przestrzeni, zwiększenie pojemności i przepustowości magazynu.
Jungheinrich realizuje magazyn typu silo o wysokości 42 m i długości 60 metrów. Rozwiązanie zapewnia maksymalne wykorzystanie przestrzeni przy jednoczesnej wysokiej wydajności przeładunkowej.
Magazyn składa się z czterech korytarzy roboczych i zapewnia miejsce na 14 tys. palet z napojami, które można przechowywać na podwójnej głębokości. Wszystkie procesy w magazynie są w pełni zautomatyzowane.
Rozwiązanie na teraz i na nieodległą przyszłość
Eksperci dostawcy zaprojektowali obiekt z możliwością dalszej rozbudowy: dodatkowe korytarze robocze można łatwo dobudować w przyszłości, nie wstrzymując pracy magazynu. Nowe rozwiązanie Jungheinrich usprawnia także transport z obszaru produkcji. W tym celu przebudowano i rozbudowano istniejący systemy przenośników: system monorail, zainstalowany w łączniku napowietrznym jest teraz sercem magazynu w Radzyminie. Transportuje on gotowe butelki do miejsc składowania – zarówno w nowym magazynie silo, jak i w istniejącym magazynie automatycznym.
– To wyjątkowe rozwiązanie. Dzięki zautomatyzowanemu magazynowi wysokiego składowania i ulepszonym trasom transportowym wyznaczamy standardy w zakresie wydajności i bezpieczeństwa. W ten sposób zapewniamy niezmiennie wysoką dostępność naszych produktów – mówi Szymon Matulka, BU Engineering Manager Poland & Baltics w Coca-Cola HBC.
Szybka praca z ładunkami nawet do 7 ton
Układnice firmy MIAS, spółki-córki Jungheinrich, odpowiadają za szybkość procesów w automatycznym magazynie paletowym: ładunki do siedmiu ton mogą być odkładane i pobierane z dużą prędkością. Również te urządzenia można w razie potrzeby rozbudować w przyszłości.
Ponadto wymieniono dotychczasowy system zarządzania magazynem (WMS). W przyszłości Coca-Cola HBC będzie korzystać tylko z jednego systemu WMS dla całego magazynu. Oprogramowanie pomaga optymalizować procesy, takie jak na przykład dystrybucję towarów do różnych lokalizacji magazynowych.
– Dla nas, w Jungheinrich, najnowocześniejsza intralogistyka oznacza wydajne i ekonomiczne koncepcje magazynowania – mówi Lech Sowiński, Project Manager Technical Sales ASRS w Jungheinrich. – To właśnie oferuje rozwiązanie, które zaprojektowaliśmy dla Coca-Cola HBC w Polsce.
Nowy magazyn wyróżnia się zoptymalizowanym przepływem materiałów. Ponieważ wszystkie rozwiązania pochodzą od jednego dostawcy, możliwa jest szybka integracja i optymalna komunikacja między systemami.
Dział: Case study
Autor: Warehouse Monitor
Grafika: Jungheinrich