DENSO zwiększa wydajność dzięki flocie robotów mobilnych MiR250
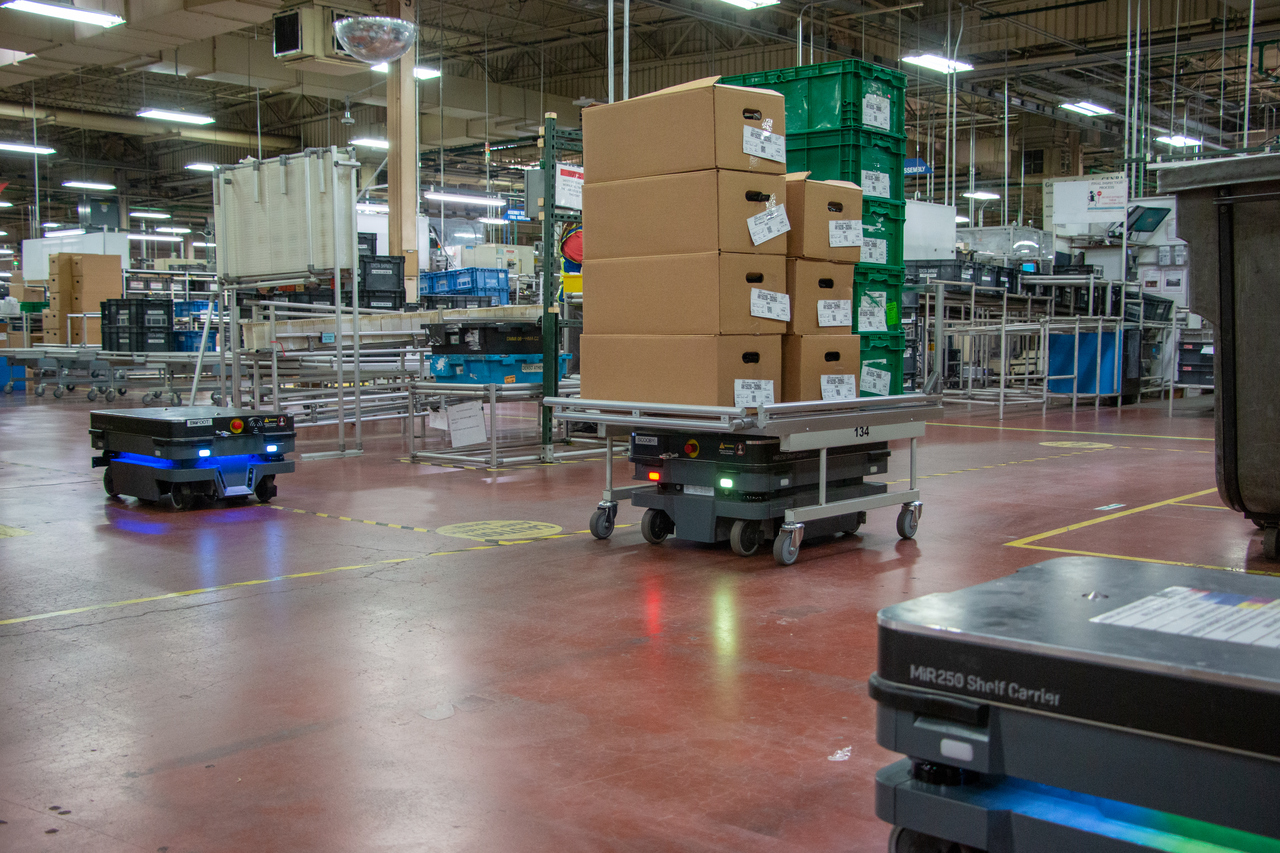
Główny dostawca części samochodowych i producent komponentów układu napędowego w Athens w stanie Tennessee osiągnął szybki zwrot z inwestycji (ROI) za sprawą zaangażowania do zadań robotów AMR marki Mobile Industrial Robots, które zautomatyzowały transport materiałów w zakładzie o powierzchni ponad 74 tysięcy metrów kwadratowych.
Firma DENSO, dostawca rozwiązań mobilnych, zwiększyła wydajność, ale również poprawiła morale pracowników i ergonomię stanowisk pracy oraz poradziła sobie z trudnościami na rynku pracy dzięki wdrożeniu sześciu autonomicznych robotów mobilnych (AMR) MiR250.
6 nowych robotów w zakładzie produkcyjnym
AMR-y zautomatyzowały transport materiałów w zakładzie produkcyjnym komponentów układu napędowego o powierzchni ponad 74 000 mkw. w Athens, w stanie Tennessee w USA. W najnowszym case study na stronie MiR można przeczytać, że od momentu wdrożenia pierwszego robota w 2020 r. w DENSO wykonanych zostało już ponad 500 tysięcy zautomatyzowanych zadań. Zwrot z inwestycji (ROI) zajął mniej niż rok, co dowiodło, że autonomiczne roboty mobilne są tym, czego firma potrzebuje, by zautomatyzować kolejne procesy w logistyce wewnętrznej.
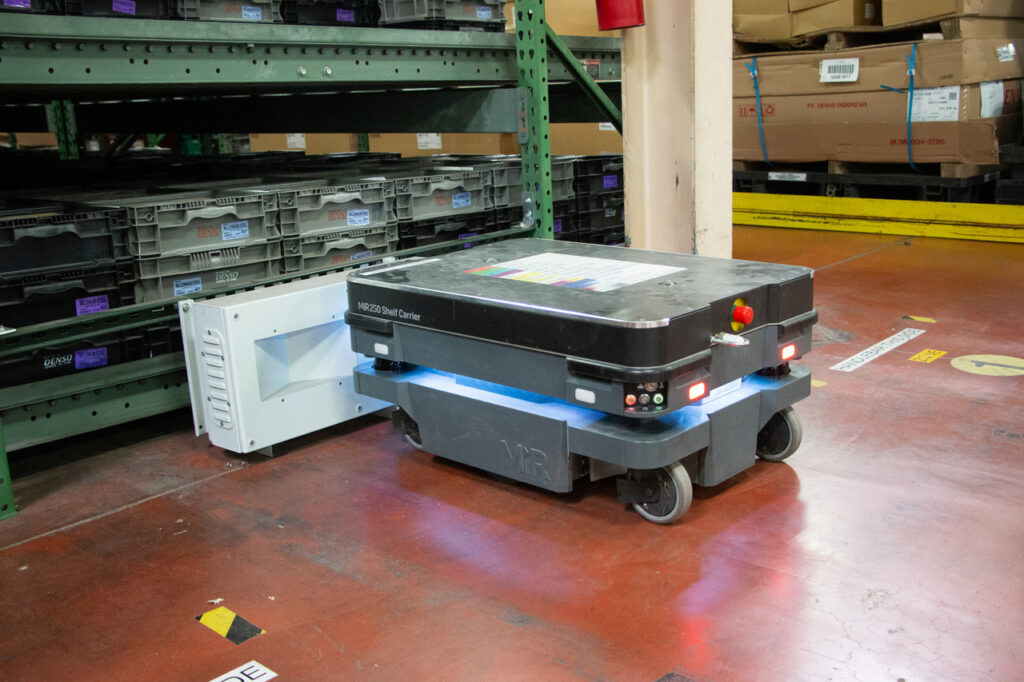
DENSO, jeden z największych globalnych klientów MiR, wykorzystuje roboty marki Mobile Industrial Robots także w dwóch innych lokalizacjach w USA oraz w trzech zakładach w Europie i w dwóch w Azji. Według Travisa Olingera, inżyniera ds. logistyki i automatyki w DENSO, firma wybrała AMR zamiast automatycznych pojazdów kierowanych (AGV), ponieważ autonomiczne roboty mobilne mogą poruszać się samodzielnie, szybko mapując pomieszczenia i zachodzące w nich zmiany, co eliminuje kosztowny problem dostosowywania infrastruktury zakładu.
– Autonomiczne roboty mobilne były oczywistym wyborem dla naszego niezwykle dynamicznego środowiska, o którym wiedzieliśmy, że będzie wymagało od robotów regularnych zmian tras – ocenia Travis Olinger. – Po przetestowaniu AMR różnych dostawców postawiliśmy na roboty MiR z uwagi na ich elastyczność, bezpieczeństwo i łatwości obsługi. MiR wyróżniał się możliwością wykorzystania połączeń REST API do komunikacji z robotami, intuicyjnością oprogramowania MiR Fleet, łatwością tworzenia map, zadań i zmian lokalizacji. Autonomiczne roboty mobilne MiR były po prostu niezwykle intuicyjne w porównaniu z innymi produktami, które rozważaliśmy.
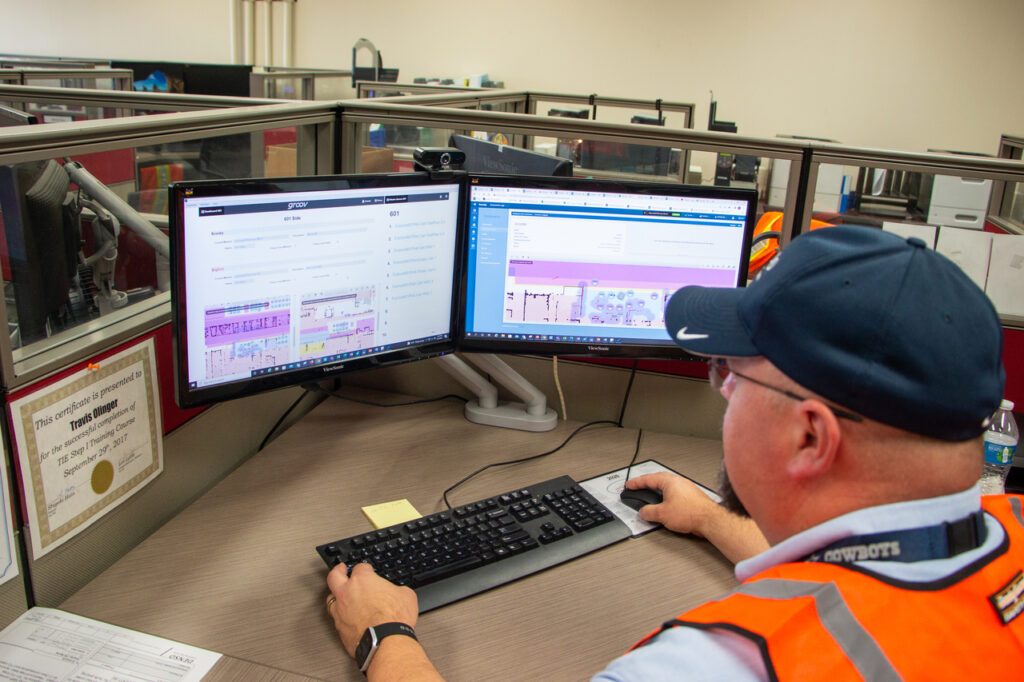
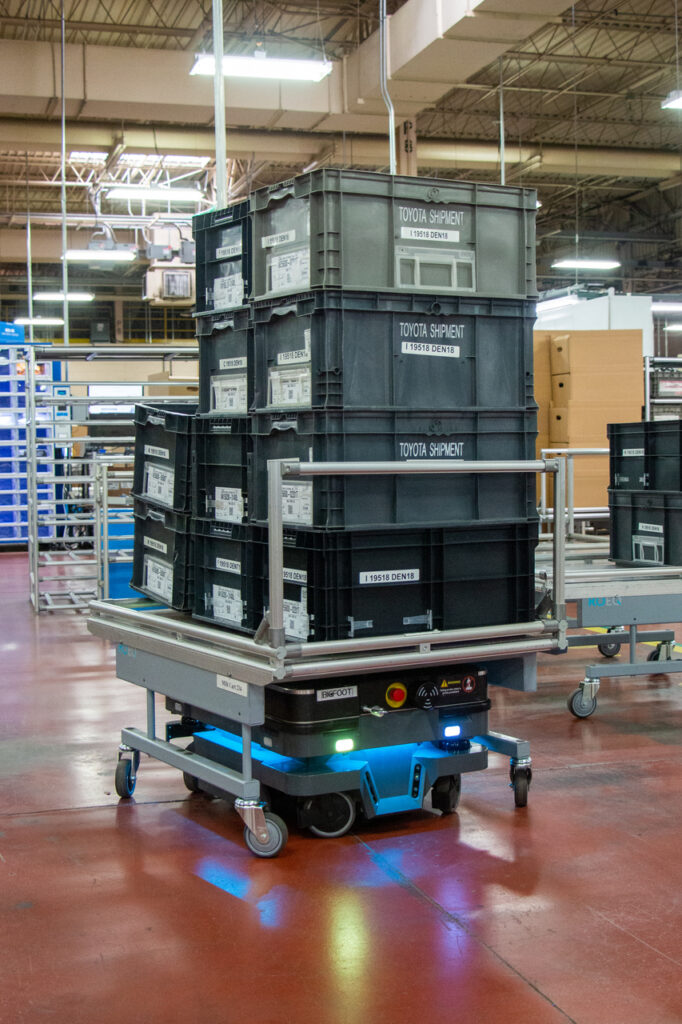
Co zdecydowało o wyborze?
Jak dodaje Travis Olinger – roboty MiR250 były szczególnie atrakcyjne ze względu na ich prędkość (2 m/s), udźwig 250 kilogramów, dostosowany do przenoszenia ciężkich metalowych części oraz możliwość poruszania się w wąskich przestrzeniach. Standaryzacja podnośnika MiR250, który ciągnie wózki partnera, firmy ROEQ, pozwoliła DENSO na szybkie rozszerzenie działalności na inne obszary przy użyciu tej samej podstawy robota i dostosowaniu jej do różnych zadań. Gdy zespół inżynierów DENSO otrzymuje dodatkowe prośby o zautomatyzowany transport, może łatwo projektować stojaki wokół wózków, pomagając zwolnić miejsce, zwiększyć elastyczność i szybciej uzyskać korzyści.
Według Travisa Olingera pracownicy DENSO pokonywali wcześniej blisko 19 km dziennie, przenosząc materiały pomiędzy obszarami produkcyjnymi a magazynem i spędzając około 60 procent czasu na obsłudze wózków. Wstępny program pilotażowy, którego celem była automatyzacja transportu w zakładzie, pomógł wyeliminować ręczne procesy, dzięki czemu szóstka pracowników mogła zostać przydzielona do bardziej wartościowych i rozwijających zadań. Wdrożenie zostało rozszerzone, by komponenty mogły być bezpośrednio dostarczane na linię produkcyjną, w celu uzyskania największej wydajności. Pracownicy szybko przekonali się do robotów w zakładzie – pojawiły się nawet prośby z innych działów, by zautomatyzować transport takich komponentów, jak materiały eksploatacyjne i części zamienne. Firma DENSO postanowiła więc niedawno zakupić dodatkowo pięć robotów MiR500 na potrzeby przyszłych zastosowań logistycznych wymagających większych obciążeń.
– Zautomatyzowanie tych powtarzalnych i uciążliwych zadań pomogło nam zatrzymać naszych pracowników – ocenia Travis Olinger. – Mieliśmy mnóstwo otwartych miejsc pracy na ważnych stanowiskach w środowisku produkcyjnym. Chcieliśmy płacić ludziom za wykonywanie dla nas pracy, dzięki której firma zarabia, a nie płacić im za przenoszenie części, co jest tylko kosztem.
Autor: Redakcja
Zdjęcia: MiR