Skuteczne metody optymalizacji przestrzeni magazynowej
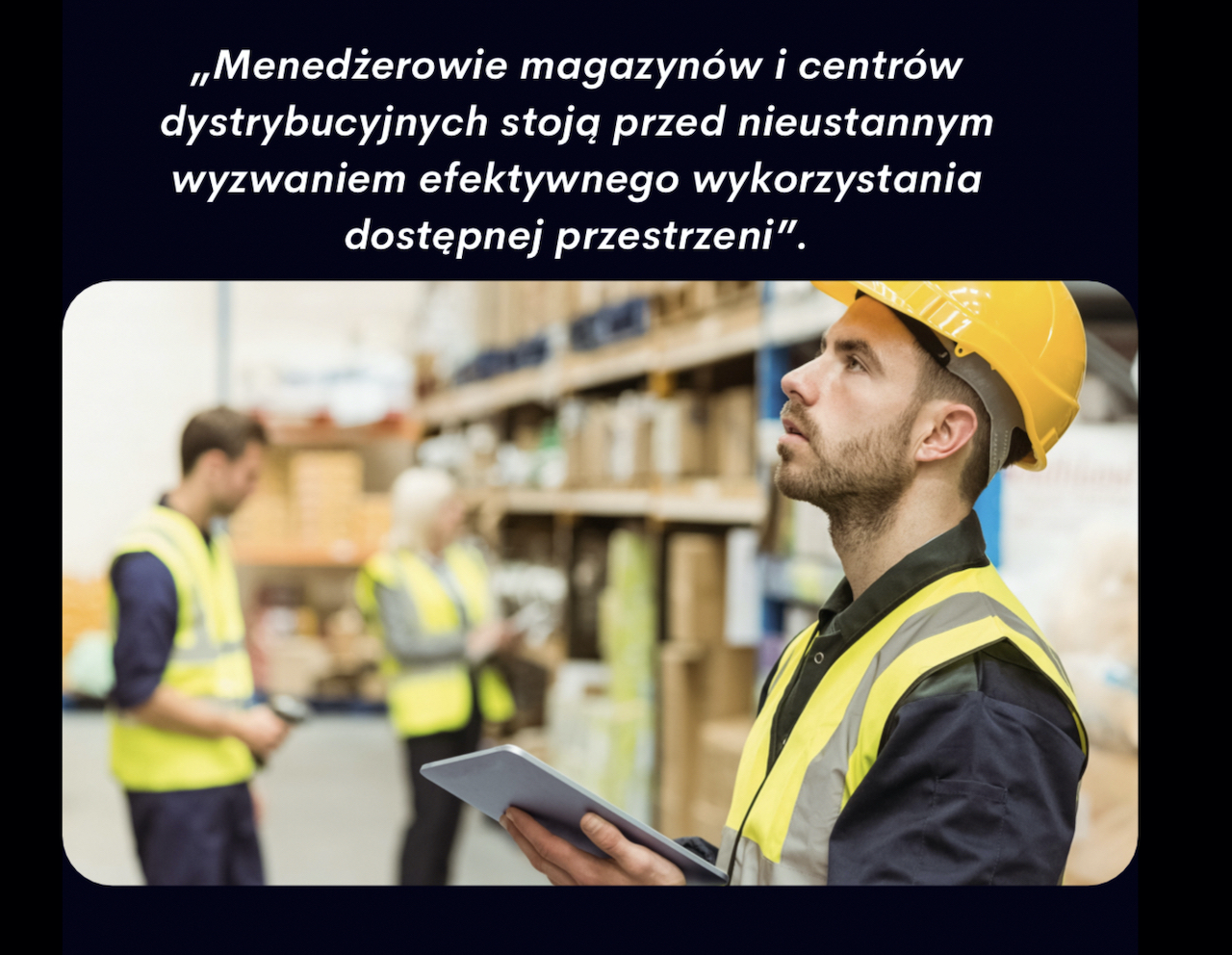
Optymalizacja przestrzeni magazynowej radykalnie wpływa na efektywność procesów magazynowych i poziom kosztów składowania. Menedżerowie magazynów i centrów dystrybucyjnych stoją przed nieustannym wyzwaniem efektywnego wykorzystania dostępnej przestrzeni.
Wśród sytuacji mogących wywołać gwałtowny wzrost zapotrzebowania na wolną przestrzeń znajdują się choćby: sezonowe szczyty zapotrzebowania na towar, budowa zapasów czy np. spowolnienie sprzedaży zwiększające ilość magazynowanego towaru.
Na szczęście istnieje wiele metod pozwalających zwiększyć pojemność magazynu bez potrzeby rozbudowy istniejącego, czy budowy nowego obiektu. Do najpowszechniej stosowanych należą:
- wybór odpowiednich regałów;
- zmiana strategii rozmieszczenia towarów;
- zmiana metody kompletacji.
Optymalizacja przestrzenni magazynowej – wybór regałów
Dążąc do efektywnego wykorzystania przestrzeni magazynowej warto zastanowić się nad doborem regałów magazynowych. Regały wysokiego składowania pozwalają np. zmaksymalizować wykorzystanie przestrzeni pionowej. Warto też zwrócić uwagę na to, aby regały dobrać właściwie dla poszczególnych grup artykułów. Jeśli w magazynie znajduje się wiele różnorodnych grup towarów, powinno znaleźć to odzwierciedlenie także w zróżnicowaniu regałów (np. regały wspornikowe dla artykułów o dużych wymiarach).
Dobór regałów to złożone zagadnienie, związane m.in. z rolą danego magazynu czy organizacją przepływu materiałów (w tym nietypowych jak np. cross-docking). Wśród wielu rodzajów regałów pomagających lepiej wykorzystać dostępną przestrzeń wymienić można m.in.:
- Regały przepływowe – są to regały wyposażone w kanały składowania o nieznacznym nachyleniu, które powoduje samoistne przesuwanie się palet po rolkach. Specyfika ich działania wymaga dostępu z obu stron regału. Regały przepływowe dobrze sprawdza się w kompletacji ładunków o wysokiej rotacji, prowadzonejzgodnie z metodą FIFO, takich jak np. żywność. Do przechowywania artykułów o małych rozmiarach stosuje się dodatkowe pojemniki.
- Regały push-back – załadunek odbywa się na zasadzie wpychania palety za pomocą wózka w gniazdo paletowe. Wyjęcie pierwszej jednostki paletowej uwalnia głębiej składowane jednostki, które dzięki sile grawitacji przesuwają do strefy załadunku.
- Regały przesuwne – są to regały mobilne pozwalające na efektywne wykorzystanie przestrzeni składowania, a także łatwy dostęp do wszystkich artykułów. Regały te przemieszczają się po wbudowanych w posadzkę szynach.
- Regały paletowe wjezdne – ich konstrukcja pozwala na wjazd wózka widłowego w kanał między poszczególnymi ramami regału. Towar składowany jest na specjalnych szynach nośnych. Istnieją dwa systemy obsługi regałów paletowych wjezdnych: z jednym korytarzem dostępu (Drive-in), oraz z dwoma korytarzami po jednym z każdej strony regału (Drive-through).
Innym rozwiązaniem maksymalizującym wykorzystanie przestrzeni magazynu są regały automatyczne.
Wybór strategii rozmieszczenia towarów
Jednym z najważniejszych i najprostszych sposobów optymalizacji przestrzeni magazynowej jest wybór odpowiedniej strategii rozmieszczenia artykułów. Wśród pięciu najczęściej stosowanych można wymienić:
Metoda ABC
Metoda ABC to najpowszechniej stosowany model przypisania miejsc magazynowych. Opiera się na analizie produktów pod względem jednego z następujących kryteriów:
- liczba wydań,
- waga/objętość towarów,
- wartość sprzedaży/wartość zysku ze sprzedaży.
Analiza ABC przebiega według tylko jednego z kryteriów. Nie ma możliwości połączenia kilku z nich jednocześnie. Według klasycznej metody ABC, wszystkie produkty dzieli się na trzy grupy o następującym udziale procentowym: A – 80%, B – 15%, C – 5%. Sprawia to, że analiza ABC często porównywana jest z klasyfikacją Pareto-Lorenza, według której 20% produktów składających się na zbiór A generuje 80% całej wartości wszystkich zbiorów. W praktyce spotkać można wiele modyfikacji tego schematu, nadających poszczególnym grupom inny udział procentowy.
W analizie ABC należy opierać się na danych pochodzących z odpowiednio długiej perspektywy czasu. Pozwala to uniknąć błędnej oceny wynikającej np. z sezonowości niektórych towarów. Produkty z grupy A powinny być umieszczone najbliżej strefy wysyłki (lub pakowania), a produkty z grupy C najdalej.
Rozmieszczenie towarów w magazynie – metoda XYZ
Metoda XYZ jest rozszerzeniem analizy ABC. Pozwala ona uwzględnić regularność zapotrzebowania na dany produkt. Według metody XYZ produkty wewnątrz każdej z grup: A, B i C dzieli się dotykowo na te o:
X – regularnym zapotrzebowaniu z niewielkimi wahaniami,
Y – zapotrzebowaniu o charakterze sezonowym,
Z – zapotrzebowaniu nieregularnym.
Dla produktów z grupy X poziom popytu jest najłatwiejszy do przewidzenia, dlatego nie ma potrzeby tworzenia znacznych jego zapasów. W przypadku towarów z grupy Z przedsiębiorstwo stoi przed wyborem utworzenia zapasów o potencjalnie długim okresie przechowywania, albo realizowania dostaw na żądanie.
Metoda ABC-FC (Fuzzy Classification)
Analiza ABC-FC jest odmianą klasycznego modelu ABC. Bazuje na wynikach podziału produktów na grupy w ramach metody ABC i regularności ich pobrań (analiza XYZ). Trzecim branym pod uwagę czynnikiem jest częstotliwość pobrań produktu. Metoda ABC-FC pozwala więc na określenie miejsca położenia produktu na podstawie trzech czynników jednocześnie.
Rozmieszczenie towarów w magazynie według metody ABC-FC jest uważane za znacznie bardziej efektywne w porównaniu z klasyczną wersją. Najważniejszą zaletą jest możliwość uwzględnienia kilku kryteriów jednocześnie. Pozwala dokonać zdecydowanie bardziej precyzyjnej klasyfikacji, zwłaszcza tych produktów, które znajdują się na pograniczu grup klasycznej metody ABC.
Metoda COI (Cube per Order Index)
COI to najprostsza z metod pozwalających uwzględnić więcej niż jedno kryterium doboru miejsca magazynowego. Analiza COI jest dwukryterialna, stanowi iloraz wielkości produktu i popytu na niego. Wielkość może być rozumiana jako masa lub objętość artykułu. Popyt natomiast wyrażony jest w sztukach.
Produkty o najniższej wartości współczynnika COI umieszcza się najbliżej strefy wydania (lub pakowania). Dzięki temu skraca się długość trasy jaką muszą pokonać najcięższe towary. Metodę COI najczęściej stosuje się wraz z systemem wolnych miejsc składowania.
Metoda EIQ (Entry-Item-Quantity)
Model EIQ opiera się na analizie trzech czynników: listy zamówień (Entry of Order), produktu (Item) i ilości (Quantity). Dzięki analizie listy zamówień można m.in. wychwycić zależności występujące pomiędzy poszczególnymi produktami, czy zidentyfikować kluczowych klientów.
W metodzie EIQ stosuje się kombinacje trzech wymienionych wyżej czynników w postaci:
- ilość typów produktów zamówiona przez klientów,
- wielkość zamówienia klientów,
- wielkość zamówienia dla każdego typu produktu,
- częstotliwość zamawiania dla każdego typu produktu.
Ograniczeniem dla klasycznych metod wyznaczania miejsc magazynowych są trudności z dostosowaniem ich do szybko zmieniającej się sytuacji w magazynie. Dlatego aby rozwiązać problem efektywnej selekcji miejsc składowania, coraz częściej sięga się po algorytmy sztucznej inteligencji, takie jak sieci neuronowe. Ich zaletą jest systematyczna, ciągła analiza i optymalizacja sposobu lokowania produktów. Im dłużej sieci neuronowe funkcjonują w magazynie, tym doskonalszy sposób przydziału pozwalają wypracować. Ze względu na swoją złożoność, praktyczne użycie algorytmów sztucznej inteligencji wymaga wsparcia przez informatyczny system magazynowy WMS.
Optymalizacja przestrzeni magazynowej – wybór metody kompletacji
Na efektywne wykorzystanie przestrzenni magazynowej wpływa także wybór metody kompletacji. Rozwiązaniem przeznaczonym dla magazynów z deficytem wolnego miejsca jest kompletacja falowa. Pozwala ona rozwiązać problem niedoboru miejsc zbiórki. Metoda ta opiera się na idei łączenia zamówień w ramach okien czasowych. Oprogramowanie magazynowe, dysponując wiedzą o dostępności asortymentu, grupuje zlecenia według przedziałów czasu, kiedy mogą być one zebrane. Program kieruje się przy tym m.in. cyklem uzupełniania miejsc magazynowych i priorytetem zamówień.
Jak wybór kompletacji falowej wpływa na pracę magazynu? Zaletą tej metody jest bardzo efektywne wykorzystanie dostępnej przestrzeni magazynowej. Wadą kompletacji falowej jest wydłużenie czasu realizacji zamówienia, co powoduje, że może ona nie spełniać wymagań niektórych branż (np. e-commerce).
Tekst: Marek Wiązowski, Quantum Qguar
Grafika: Warehoue Monitor